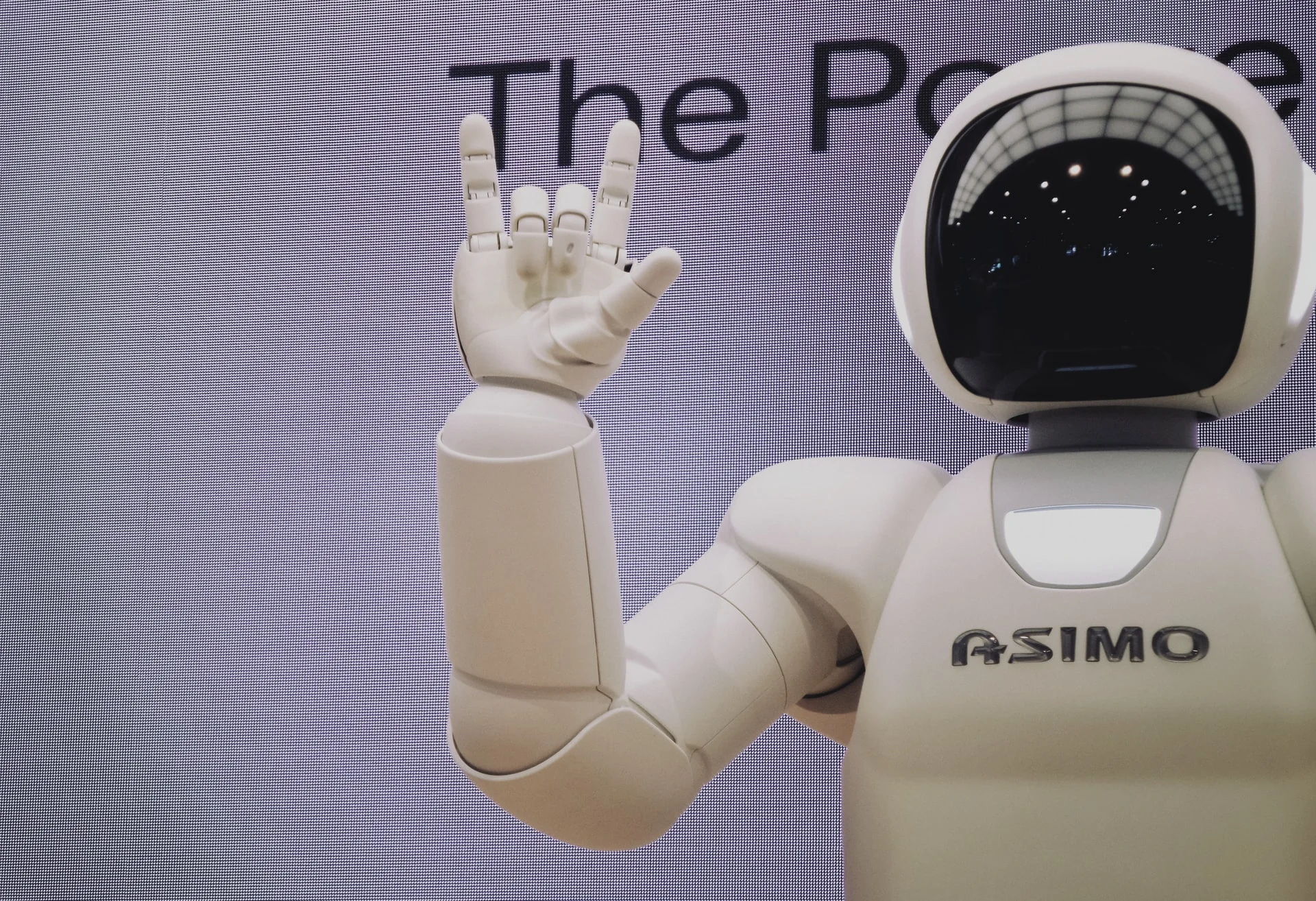
The role of RPA in logistics and transportation
According to a survey among 269 supply chain professionals, fewer than 10% of surveyed respondents have achieved near-full automation in their key supply chain functions. Such a high level of automation helps those digital leaders efficiently manage customer demands and be less affected by supply chain disruptions. RPA in logistics is one of the ways to increase efficiency and unburden employees by automating mundane tasks.
RPA is a software bot that mimics human interactions with services, systems, and applications. RPA in transportation and logistics can perform such routine tasks as entering shipment details into a transportation management system (TMS) or filling out a bill of lading (BOL). A logistics operator can spend all day on such trivial tasks. Why not make digital solutions perform simple rules-based jobs while people use their cognitive skills to move the business forward? That’s exactly why companies are choosing RPA and other workflow automation technologies to be among the most successful supply chain companies and drive digital transformation in logistics.
Define and automate repetitive tasks that stall your logistics workflow
Our RPA servicesWhy logistics companies are turning to RPA
Logistics managers deal with lots of data scattered across different software systems — TMSs, warehouse management systems (WMSs), enterprise resource planning (ERP) systems, customer relationship management (CRM) systems — as well as across Excel spreadsheets and paper documentation.
Plus, data volumes are growing exponentially in the logistics domain, and companies drown in many monotonous copy-and-paste and drop-and-drag tasks that take time but don’t add any value to the company. Employees tend to make many mistakes while performing such high-volume tasks, as they may easily get distracted or tired. RPA software bots can unburden employees from most of this routine work and can perform it much faster, 24/7. In the meantime, employees can have more time to manage exceptions, perform analytical work, and deal with customers’ issues.
Take an example of Levi Strauss & Co., an American clothing company that combines many famous brands such as Levi’s, Beyond Yoga, and Dockers. They managed to automate 25,000 hours of work with 45 in-house bots, mostly by automating data entry and data validation tasks. The company uses RPA bots in IT, sales, product development, distribution, and logistics. Such a result allows Levi Strauss & Co. to increase sales while saving time and resources on repetitive tasks.
With automation solutions, businesses can work faster, efficiently reprioritize their goals, and define root causes of major issues before they escalate. Thus, automation gives space and time to alleviate the burden of customer service teams, reallocate budget (e.g., to modernize warehouse operations), and help employees do their job more efficiently. Eventually, you will have time for a business growth strategy that will help you outpace your competitors and win over customers.
Learn about management by exception software in logistics: Requirements and must-have functionality
Read the articleKey business benefits of RPA in the logistics industry
The benefits you get thanks to robotic process automation in logistics depend on the type of business processes you choose to automate. However, there are some general perks of this technology.
- Shift from data entry to strategic planning. By automating routine tasks, your supply chain management teams get a chance to focus on important strategic goals related to customer service, marketing, and sales.
- Satisfied clients. Automation allows you to process orders and deliveries quickly. Thus, customers can place more orders than usual and receive them faster. RPA software may help you exceed your customers’ expectations and satisfy the needs of even the most demanding customers.
- Productive workforce. With RPA technology, you can give your employees more time for unlocking potential and encourage them to contribute to your business. Plus, if you allow your employees to make decisions that benefit the company, your employees will be more loyal.
- Error-free document management. Imagine eliminating all typos and all other human errors from your documentation for good. Sounds alluring, doesn’t it? Then consider this: software bots usually achieve 100% accuracy in extracting, entering, creating, and processing data.
- Fast development and deployment. On average, RPA deployment for processes of medium complexity takes much less time than developing standalone applications and systems. This is mainly because one software bot is built to perform one task or process. And even if your company’s processes grow and you implement more and more bots (there are companies that use more than 50), the implementation is gradual and doesn’t require huge investments at once.
Implementing RPA software makes your business environment more customer-centric. And as you free your employees from the routine, you make space for growth.
Common use cases of RPA in logistics
There are the following RPA use cases in logistics:
Order fulfillment
Order fulfillment is an example of a time-consuming process that looks the same in many supply chain organizations. Software bots can process one order in two minutes instead of the 20 minutes a human would spend on the same task. An RPA-powered system can receive an order from a customer, check the stock, and invoice the customer via email if the products ordered are in fact in stock.
Thus, companies can process more orders in a working day and even beyond working hours. Software bots can also migrate data between different supply chain systems like TMSs, WMSs, and ERPs.
Shipment scheduling and tracking
Composing feasible and accurate shipment plans constitutes a big part of a logistics company’s responsibilities. Intermodal shipments that involve more than one means of transportation may require even more accuracy than, for instance, truckload shipments.
RPA technology can take charge of shipment scheduling and tracking. With RPA in transportation, you can quickly fill out documents, assign orders to the right transport, and track shipments from departure to destination.
Appointment scheduling
Scheduling appointments with shippers, receivers, and carriers can also be a tedious task, with many back-and-forth emails for confirming or declining appointments.
You can integrate RPA for carriers into your transport management system or yard management system to schedule appointments and send timely emails to all participants. Plus, software bots can notify participants of upcoming appointments and status updates.
Document management
Logistics is often associated with piles of documents like BOLs that ensure the receiver gets all the requested products, and proofs of delivery that ensure the shipping company that the receiver got the requested products within the requested time frame.
Along with developing a logistics delivery platform, you can create bots responsible for retrieving data from all incoming and outgoing electronic documents. Bots can even open email attachments, identify document types, extract critical information, and move documents to the company’s database. With robotic process automation for mobility and logistics, it becomes unnecessary to manually rekey data from one document to another or send dozens of repetitive emails to shippers, receivers, and carriers.
Warehouse and inventory automation
Continuous data entry and reports consolidation in warehouse and inventory management systems take up much time and hardly bring any value. To optimize such time-consuming workflows, SF Supply Chain uses UiPath’s RPA solution for data processing in their warehouses. They’ve adopted RPA bots to automate inventory management by performing such tasks as automated courier data entry, order printing, wave picking, and parcel collection, which resulted in 74,000 working hours saved.
Last-mile delivery optimization
Last-mile delivery directly impacts customer satisfaction, as it’s either quick and efficient or prolonged and error-prone. In the first case, your customer gets their orders to the doorstep when expected or even faster. In the second case, their parcel gets delivered to a different doorstep, is lost, or is delivered so late that customers won’t even order any more from you. To always fall within the first case category, RPA can be of help. RPA bots can help last-mile operators by optimizing supply chain operations and generating the most optimal route plans automatically while saving planning cycle time. Plus, multiple bots can work simultaneously to cover a large number of deliveries.
Freight audit and payment
A report on freight audit automation states that, on average, companies pay up to 10% more in freight expenses due to billing errors. By automatically verifying voluminous freight invoices across multi-modal transportation means, contract terms, taxes, and shipping documents, RPA bots can streamline the freight auditing process and ensure accurate payments between different supply chain parties. Manual checks require much more time and resources, potentially leading to frequent errors. Thus, with the help of RPA for transportation and other automation technologies, companies can avoid freight fraud, invoicing errors, and excessive and unexpected expenses.
You can create separate bots for performing routine and consistent processes in your logistics organization. You can even make them smarter by empowering them with artificial intelligence (AI) or machine learning (ML). These technologies can transform your bots into voice assistants or chatbots that can make certain decisions themselves, such as sending an additional explanatory email to an unsatisfied customer.
Learn how to streamline your supply chain at different management levels
Supply chain optimization articleReal-world examples of RPA adoption
Many modern companies have already started reaping the benefits of RPA in the shipping industry. Below are a few examples that prove this.
Redwood Logistics, a third-party logistics (3PL) company, is using RPA to automate the following processes:
- Retrieving documents from emails
- Updating statuses in multiple software systems
- Tracking and tracing shipments
- Sending exception notifications
- Determining the estimated time of arrival (ETA) for shipments
Before implementing RPA technology, Redwood Logistics employees had to manually track thousands of monthly shipments. This process was extremely time-consuming and did not add value for the company. Manual shipment management was also error-prone, and if, for example, a parcel was lost on the way, managers had to take reactive measures to deal with the issue. RPA allows for making proactive decisions that safeguard the company from some obvious bottlenecks.
RPA enables the company’s managers to provide customers with full shipment visibility, freeing up the workforce for more customer-related tasks that help to increase customer satisfaction.
RPA adoption yielded the following outcomes for Redwood Logistics:
- 55% increase in revenue within 24 months after adoption
- Increase in monthly shipments from 3,500 to more than 12,000.
Learn how to digitalize value-added warehouse services at your 3PL company
Read the articlePITT OHIO
PITT OHIO is a transportation company offering less-than-truckload, truckload, and other supply chain solutions in the US Midwest and Mid-Atlantic regions.
The company’s customer service representatives (CSRs) had to process many customer requests manually by re-entering shipment details into multiple software systems while manually logging into each system.
Integration of RPA for trucking helped the company automate most manual business processes. Software bots can now extract shipment details from incoming emails and add them to all the company’s systems in several minutes.
PITT OHIO gained the following results thanks to automation:
- 95% productivity increase of CSRs
- 100% accurate invoice creation
- 100% elimination of routine processes that CSRs perform
In both Redwood Logistics and PITT OHIO, RPA adoption resulted in a huge productivity improvement. And to achieve similar results, you don’t have to automate all manual processes in your organization at once. Even a few bots can make a difference and boost your employee and customer satisfaction.
If you feel inclined to give RPA technology a try, you need to figure out common challenges that can prevent seamless RPA adoption.
Challenges of implementing RPA in logistics and supply chain
Integrating RPA software into your business workflow can pose difficulties. However, they can be easily mitigated if considered in advance.
Data preparation. A Supply Chain Integrity Outlook 2025 report reveals that inaccurate data is one of the biggest threats to the supply chain. Inaccurate data can lead to many logistics issues, such as misloads, delivery delays, and label inaccuracies. 59% of respondents (among 1,000 surveyed supply chain professionals) say that their organization isn’t resilient enough to tackle disruptions and changing customer demands. Achieving high data integrity directly impacts supply chain visibility, resilience, and reliability.
Capturing, cleaning, and consolidating high-quality supply chain data is the first step to take before adopting any automation technology, and RPA isn’t an exception. To enable high-quality data processing, we analyze the reliability of your data sources, validate data quality, and build custom data pipelines that deliver accurate supply chain data in real time.
Data security. RPA bots work with your business data, which can contain sensitive elements such as customer addresses and payment information. To ensure secure data handling and avoid data breaches and theft, you should work out a cross-company data governance framework. It involves developing a set of policies for data access, ownership, sharing, and acquisition. Beyond that, for the utmost RPA bot security, we:
- enable rigorous security checks during the RPA development process
- restrict bot access to only relevant data
- assign each bot a unique identifier for simplified tracking
- regularly audit RPA performance
- gather information on bot operations into accurate logs
Integration with legacy systems. Many logistics enterprises still use outdated yet business-critical software systems that don’t provide APIs for seamless data retrieval and integration. It may seem that automation technologies wouldn’t be suitable for these systems. However, custom RPA bots can be programmed to work with legacy software and move data in and out without any risk of business disruption. Plus, custom logistics software in the form of RPA is a possibility to speed up employees’ work with outdated systems, without the immediate necessity to modernize legacy software. This gives you time to come up with an iterative software modernization plan while already benefiting from the perks of automation.
Change management. RPA can cause resistance in the organization, as often this technology can be misleadingly perceived as a substitute for human workers. Therefore, before announcing the adoption of this technology, you should have a clear business vision of how RPA integrates into your daily logistics workflow and how your employees will work alongside it, and what benefits they can get. As is often the case when adopting new technology, business owners think of the benefits for the business (e.g., saved working hours, increased operational efficiency, and reduced costs), but taking into account people who will use this technology should be a priority as well.
By focusing on accurate data management and tangible people benefits, you’ll be able to beat any RPA challenge and derive the most value out of this technology.
Leverage BI and data visualization tools to increase supply chain visibility
Logistics dashboards articleWhen to consider RPA for logistics
To know when and where you should apply RPA bots, analyze which manual and rules-based processes are the most time-consuming and burdensome in your company. Start with automating them to obtain quick and tangible results (as Redwood Logistics did). To help you with choosing the right processes for automation, here are a few questions you can ask yourself:
Let’s have a look at what stands behind these questions.
- What kind of process is this? Identify core time-consuming and monotonous processes in your organization, like report generation, order processing, shipment tracking, and folder and file management.
- Is this process rules-based? Simply put, rules-based processes can be referred to as “If” statements, meaning that “If X happens, THEN do Y.” A certain action triggers the next action (and so on) until the process is complete.
- How complex is the process? Define the process complexity by the steps a human takes to complete it. Basically, if your employees have to open up to four systems or applications and take fewer than 50 steps, then this process would be considered small. If a process takes more than 50 steps and more than four applications or services, then it’s a medium-complexity process. Large processes require more than four applications and more than 100 steps.
- Do operators often have to manage exceptions to this process? You can review how your employees handle routine processes and see how often certain exceptions to these processes occur. This way, you’ll define which processes will still require a lot of human intervention even when automated and which won’t.
Thus, after answering those questions, you’ll have a list of routine, error-prone processes of small or medium complexity. You’ll then need to prioritize them and define which ones consume most of your employees’ time and your organization’s money, and take them as the first ones to develop software bots for.
Why Yalantis as your RPA integration partner
Developing a custom RPA may require more time, resources, and investments than integrating a pre-built software solution. Still, there’s no ready-made service that will offer you the same level of flexibility and adaptability as a custom solution. Here’s how Yalantis can help develop your own software bot.
- Assistance with setting clear expectations for RPA adoption. Going for RPA and other supply chain automation technologies only because it’s trendy isn’t wise. Identify what you want to achieve with this type of software and consider if it applies to your business needs and regular workflow. An RPA solution is meant to optimize your business processes and make your employees more efficient. Start small and at first implement only one or two bots to perform the simplest tasks to see if this software works for you.
- Future-proofing RPA bots by laying the foundation for AI and ML. Plain RPA software can be rather straightforward and limited. Enhancing it with AI and ML capabilities opens more opportunities for your company. For example, such empowered software can process handwritten documents, analyze images and photos, answer your customers’ typical queries, and unburden your support team. You can opt for building RPA with AI and ML technologies right away and not even wait for future software updates.
- Long-term development partnership. Digitization is a fast-evolving phenomenon, especially when it comes to technologies that can perform tasks instead of humans. Consider long-term cooperation with our development team so we can support, maintain, and improve your software promptly. With your in-house business development teams, we can compose an RPA center of excellence (COE) to efficiently measure RPA ROI and its impact on your business performance.
At Yalantis, we always offer long-term support for our clients after the development and deployment stages. Plus, the logistics domain is one of the core areas of our expertise, so our team knows well all the pain points and peculiarities of supply chain and logistics operations. You can rely on us for digital transformation support for your business. We’re eager to help you streamline all inefficient logistics processes with advanced automation tools.
Need a custom solution for logistics workflow automation? We can help
Explore our expertiseFAQ
What supply chain management processes can be automated with RPA?
RPA is best suited for repetitive, rules-based tasks that consume time but don’t require decision-making. In logistics, that means automating tasks like order processing, shipment scheduling and tracking, appointment coordination, document management (like BOLs and PODs), warehouse reporting, last-mile delivery planning, and freight audit and payment.
For example, a software bot can pull shipment details from an email, enter them into your TMS, assign the right carrier, and even send an ETA update to your customer — all in a few seconds.
How long does an RPA project take?
On average, you can launch your first RPA bot in 4 to 8 weeks if the process is of small or medium complexity and well-documented. More complex scenarios involving multiple systems, unstructured data, or legacy integration may take up to 3–4 months. But RPA is highly modular; you don’t need to automate everything at once. Many logistics companies start with a single process, like document extraction or status updates, and scale up gradually.
Is RPA secure for handling sensitive logistics data?
RPA bots can be set up with strict access permissions, unique credentials, and detailed activity logs, making their operations transparent and traceable. Leading logistics RPA solutions follow enterprise-grade security practices, and at Yalantis, we build custom bots with built-in compliance features.
To protect sensitive data like delivery addresses, payment records, or shipping manifests, we also recommend creating a cross-company data governance framework. That means you stay in control of who accesses what and how.
What’s the difference between RPA and AI in logistics?
In logistics, RPA might enter delivery info into your WMS or send a POD email to a client. AI might predict delivery delays based on traffic and weather or recommend optimal warehouse layouts. When combined, they’re even more powerful. You can build smart RPA bots that analyze handwritten documents with AI or answer customer questions as intelligent assistants.
Rate this article
5/5.0
based on 1,337 reviews