SaaS-based transportation management system
Discover how we developed a cloud-based transportation management system that simplifies and accelerates user onboarding, improves route planning and monitoring, and enables fast and automated problem-solving.
-
industry
Logistics
-
Country
USA
-
Team size
>10
-
Collaboration
2019
About the client
Our client is a US-based logistics company that specializes in shipping goods across the entire country.
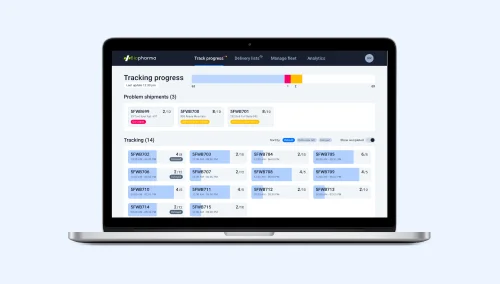
Business context
When the client approached Yalantis, their business was actively expanding and experiencing problems with order, employee, and delivery management. Available software didn’t meet their specific needs. That’s why our client decided to create a custom solution to solve the following challenges:
- User onboarding was time-consuming
- Manual route building took up to six hours a day
- Routine communication and inefficient problem-solving took up to three hours a day
Solution overview
-
The Yalantis team developed a SaaS-based transportation management system called Smart Logistics. It helps the client streamline their operations, provides end users with an intuitive and convenient work environment, and simplifies the onboarding process.
Improving communication with automation
To reduce the time for routine communication between a warehouse and a logistics manager, we integrated with existing warehouse solutions and enabled real-time automated delivery list updates. When a warehouse manager marks a delivery list as done, a task automatically appears for a logistics manager to form a route.
-
Optimizing and accelerating route management and monitoring
To ensure seamless delivery route management and monitoring, our team implemented a comprehensive dashboard with:
- automated route management. Managers can overview delivery statuses and select any vehicles that can’t meet the delivery timeframe. The system will then suggest alternative vehicles that can deliver within the required timeframe based on specific delivery requirements.
- an algorithm-driven optimization system. When delivery lists are ready, the system automatically creates routes for them with the optimal price/speed ratio in just a few minutes.
- draft management. It’s possible to save drafts when setting up routes to try different options and choose the most suitable.
- a real-time notification center. The system notifies of any errors, such as overload or the inability to meet a delivery timeframe.
-
Enhancing problem-solving through real-time shipment status updates and effective UX
To optimize logistics problem-solving, Yalantis specialists:
- designed route cards. Route cards are UI elements that contain brief information on a particular delivery route with real-time status updates.
- provided real-time status visibility. Administrators instantly see notifications about problems along the route: the card for a problematic route appears on top of others, along with a problem type description. The system also understands when a driver is behind schedule and marks the associated route card as delayed.
- accelerated problem-solving. A driver can choose an identified problem from a drop-down list in their driver app. A manager will be instantly notified of it and can choose a solution right in the route card.
-
Enabling quick onboarding
We designed an easy five-step onboarding process for Smart Logistics, where the client only needs to:
- provide details such as the company’s name and logo
- create a directory with main warehouses grouped by city (manually or with a .csv file)
- add databases of vehicles with their characteristics and of drivers with their contact details, work hours, and category and type of driver’s license
- add delivery points with names, contact details, and any notes for couriers
- add names and contact details of employees from the logistics department and distribute roles and access levels
Value delivered
Smart Logistics brought our client the following results:
-
Smart route optimization. With the new TMS, it takes just about 30 minutes from receiving a delivery list from a warehouse to returning routes (instead of several hours).
-
Fast and automated problem-solving. All routine problems are solved through the system instead of by making lots of phone calls, with real-time notifications, automated status updates, and a smart dashboard.
-
Seamless onboarding. It takes just a few minutes to add a new employee to the system and a few more minutes for them to understand how the system works.
Automate your transportation routine and problem-solving
Yalantis will create a custom transportation management system to help you meet market demands and achieve your business goals.