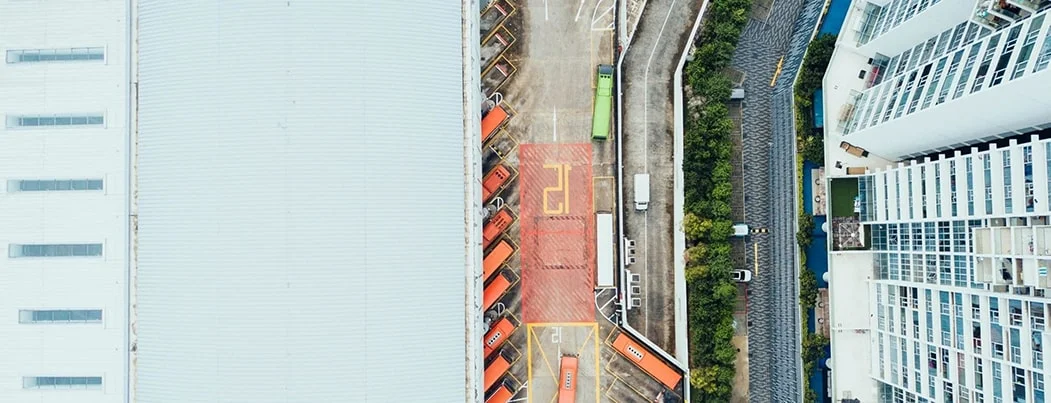
How a yard management system can boost yard and warehouse efficiency
Digitization can breathe life back into your yard and help it operate as a coherent element of your supply chain. Many logistics businesses are switching to technological solutions and implementing yard management systems (YMSs) to automate and streamline yard processes and enhance warehouse efficiency management. The global market for dock management and yard management systems is expected to rise from $3.3 billion in 2020 to $7.9 billion by 2027 according to a report by Research and Markets.
Further on, we’ll show you how an advanced YMS can help your organization:
- eliminate lots of repetitive and time-consuming processes in your yard
- predict and prevent possible disruptions in the yard workflow
- make informed decisions as to whether you need to hire more workers, purchase more spotters, sign contracts with more carriers, etc.
First, let’s outline the most common yard management issues that logistics companies face.
Pain points in the yard across industries
According to The State of Yard Management 2021 Industry Report by FourKites, the biggest pain points in the yard across industries are manual processes and locating equipment. Let’s discuss these and more pain points in detail.
#1 Manual processes
The biggest portion of manual work falls upon those responsible for the gate, appointments, and dock management. For instance, there is usually a guard at the gate to manually check trucks in and out. Before letting a truck driver in, the guard has to check the driver’s license, ensure that the driver is on time, and notify the dock crew that a new truck has arrived for unloading.
Delays in a guard’s work lead to a lineup of idling trucks and drivers, burning fuel and time. Misunderstandings between truck drivers and guards, who may speak different languages, might prolong such delays. Plus, logistics managers often make shipment appointments with carriers via emails or phone calls. This approach is highly inefficient and error-prone, often leading to missed and delayed inbound and outbound shipments.
#2 Locating equipment
Another common issue is finding equipment in the yard. For instance, without proper yard visibility, a yard driver can spend much time searching for the right trailer to take to the dock. This search may result in many redundant moves and inefficient use of spotters. Additionally, if a trailer’s position isn’t updated in real time after unloading or loading, it will likely cause delays in outbound shipments.
#3 Operational costs
Excessive yard expenses are one more pain point for supply chain businesses. With an inefficient yard workflow, trailers often aren’t loaded on time and linger in the yard while incoming trucks wait at the gate. Such inefficiency results in detention and demurrage fees for shippers.
Plus, improper task allocation between yard drivers and dock personnel leads to overtime, worker discontent, and the necessity to hire more new workers.
#4 Absence of operational yard analytics and metrics
Without automated analytics tools to measure and evaluate yard performance in a logistics company, it’s difficult to identify areas for potential growth and the root causes of yard inefficiencies.
YMS as a solution to your yard pain points
This is where a proper YMS gives a helping hand, as proven by the example of Alpro, a manufacturer of plant-based dairy alternatives that implemented a yard management system in its workflow.
Once Alpro’s YMS notifies a truck driver to proceed to the gate, stacker cranes (operating with automatic handling and storage systems) in the warehouse automatically prepare the right pallets with goods for loading the truck. This reduces the whole turnaround process to 30 minutes. For the food and beverage industry, order execution time is especially critical, as consumers expect only fresh products on supermarket shelves.
Despite all the possible benefits of a YMS, some logistics companies are still reluctant to implement one. Let’s figure out what’s stopping them.
Common misconceptions about YMSs
A 2020 FourKites survey of 375 supply chain professionals reveals that 92 percent believe a YMS could improve their performance. However, only 25 percent use a yard management system of any kind. The only exception is in retail, where 41 percent of respondents already use a YMS.
Here are a few common misconceptions that stop companies from implementing yard management systems:
- There’s no need for a YMS if the shipment volume is small. Talking Logistics’ analyst Adrian Gonzalez says that some companies believe that to warrant investment in a YMS, their shipment volumes should be much bigger and yard operations more complex.
Reality. A proper YMS can streamline the work of even small and midsize logistics yards. A YMS can close lots of typical supply chain issues like long trailer wait times, unproductive personnel, and ineffective dock scheduling. - A WMS is enough for handling basic yard operations. Many shippers manage their yard entirely with the help of yard-related functionality in their WMS and believe it’s sufficient.
Reality. Yard functionality in a WMS is often limited and, for instance, may not provide real-time updates on a trailer’s location in the yard. Proper yard management strategies are just as critical for successful supply chain execution as proper management of warehouses and transportation, especially given the conditions resulting from the pandemic and e-commerce boom. You can also check out our article on space optimization in storage and transport facilities amid the e-commerce surge. - Shifting to a YMS may disrupt the usual workflow. As implementing new software takes time, some companies anticipate that it may interrupt the yard workflow, leading to significant financial losses.
Reality. There’s no necessity to switch to a new workflow all at once. You can choose a gradual deployment model and split your employees into small learning groups so that implementing the YMS doesn’t feel like a bolt from the blue. Find out how you can foster employee learning in our blog post on custom LMS development.
To help you understand what a yard management system can do to cover your business needs, let’s consider the main purpose and critical functionality of a YMS.
Read also: Improving Warehouse Productivity: 5 Indicators You Need It
How does a YMS work?
A YMS is a software system that operates as an intermediary between a company’s warehouse management system (WMS) and transport management system (TMS). A YMS optimizes the planning functionality of these systems. The primary purpose of the YMS is to enhance yard and warehouse efficiency and operations by managing the flow of all inbound and outbound vehicles.
A YMS optimizes five major yard processes:
Basic functionality of modern YMS software
Let’s have a look at the core functionality that proper YMS software should include to add real value to your logistics business.
Gate management
A YMS’s gate management functionality facilitates truck drivers’ checking in and checking out at the gate. When drivers arrive at the gate, they can enter their appointment numbers into a self-service touchscreen kiosk near the gate that is integrated with the YMS. The YMS can then confirm appointments, assign trailer parking spots, and open the gate.
The system tracks all movements of a truck in the yard from the moment it enters until it leaves. Additionally, if you’re receiving goods from your shipper, the latter can send an advanced shipment notice (ASN) to your YMS that gives the system all necessary information about the driver and the trailer’s load before the shipment arrives.
Appointment management
Supply chain industry experts say that a modern YMS should have online appointment scheduling functionality. This allows shippers, receivers, and carriers to quickly schedule and confirm inbound and outbound shipments, replacing time-consuming phone calls and emails.
According to customer reviews, it takes just seconds to book a shipment appointment with an online appointment tool. Each appointment can also have statuses indicating whether the delivery will be on time or late. Appointment management functionality also allows shippers, receivers, and carriers to alter the schedule if needed and promptly notifies all parties of any changes.
Dock scheduling
An advanced YMS should also allow logistics managers to create a schedule for dock use, improving warehouse efficiency. Thus, yard drivers and dock workers can know the exact time when a trailer must be at a dock door for loading or unloading.
This increases the productivity of the dock crew, yard drivers, and spotters while avoiding delays in inbound and outbound shipments. Additionally, yard managers can set the time range for loading and unloading trucks based on shipment criteria like quantity and product type.
Real-time visibility of yard assets
This type of YMS functionality helps you be aware of the actual location of all your yard assets. With RFID (radio-frequency identification) tracking devices placed on trailers and spotters, your YMS can get real-time updates of all yard movements. This will ensure a well-coordinated workflow in your yard, eliminating the need for manual yard checks and searches for yard assets.
Task management
A YMS might send task messages to the yard and dock personnel. For instance, yard drivers might receive timely notifications to in-cab devices on the movements they need to complete in the yard. The dock crew can get notified on rugged mobile devices or at their workstations once a trailer arrives at the dock door.
A YMS with functionality for distributing and prioritizing tasks among yard and dock workers can decrease idle time, increase productivity, and consequently eliminate the need for hiring new workers.
Alert system
With timely alerts in your YMS, you’ll know about late truck departures and arrivals, which trailer is approaching its return deadline, etc. Plus, if you work with cargo that needs constant temperature control, you might include a reefer monitoring system in your YMS that sends alerts if the temperature in trailers exceeds the permissible range in order to prevent damage to perishable goods.
Analytics and operational reports
Analytics tools in a YMS can be beneficial in many ways. For example, if a yard’s productivity is decreasing, analytics and reports can help logistics managers identify areas for improvement.
Integrations with external systems
Most YMS vendors provide open API gateways to enable integration with your existing supply chain software, such as warehouse management systems and transportation management systems. For instance, incoming data from a WMS can contain information about outbound shipments, while a TMS can provide information about expected arrival times or vehicle data like maximum volume and load, trailer type (flatbed or reefer), etc.
Above, we’ve mentioned only a basic set of features and integrations each YMS should contain. Lots of YMS vendors also offer additional functionality and customization tools. Here is an example of an extra but currently common YMS integration.
Integration of IoT devices. Shippers tend to incorporate in their logistics workflow such technology as cameras, sensors, drones, and robots. Integrating any of these devices with a YMS can help you automate more yard operations, enhance your yard’s monitoring capabilities, and provide more data for yard and warehouse analysis and improvement.
As you’re now familiar with the basic functionality and integrations of a YMS, you can decide what fits your business more: a custom solution or a ready-made one. In the next section, we’ll talk about YMS solutions available on the market.
Types of ready-made YMS solutions
There are different types of YMS software that you can implement in your logistics business. Let’s consider the most common types.
Standalone YMS solutions
Some vendors offer full-fledged standalone YMS solutions. For example, C3 Solutions provides two separate YMS modules: C3 Reservations for dock scheduling and C3 Yard for yard management. Plus, dock and yard personnel can interact with the progressive C3 web application via their mobile devices.
Other vendors such as FourKites, PINC, Cypress Inland, Yard Management Solutions, and Exotrac focus more on the real-time visibility of yard assets. For example, Exotrac offers a customized YMS for different logistics industries including manufacturing, chemical distribution, food distribution, and 3PL.
Standalone YMSs offer the most large-scale functionality of all ready-made solutions. Plus, some vendors of these systems provide 24/7 support and timely updates.
YMS add-on modules
Many vendors of supply chain solutions offer to integrate a YMS module with their WMS or TMS. For instance, Manhattan Associates, 4Sight, Zebra, Aptean, and Blue Yonder provide YMS modules that work well with their WMS and TMS solutions or that can integrate with yours.
Vendors of enterprise resource planning (ERP) software like SAP and Oracle also offer YMS modules among their services. Add-on modules provide full basic functionality that includes dock scheduling, gate management, real-time visibility over yard assets, and yard driver task optimization.
It’s time-consuming but achievable to find the most appropriate ready-made solution for your yard. The question is whether a ready-made YMS is your cup of tea. To help you find out, let’s discuss the major drawbacks and advantages of such solutions.
Read also: Choosing Transport Management Software: Types of TMSs and Must-Have Functionality
Drawbacks of existing YMS solutions
After checking customers’ reviews of some of the ready-made YMS software solutions, we’ve compiled a short list of the most common disadvantages.
Limited customization capabilities. The most obvious but critical drawback of all ready-made solutions is a low level of customization. To fulfill their individual needs with existing solutions, organizations often want to customize certain features. However, this is often a challenge. For example, FourKites customers say that the support team takes much longer to handle issues with custom features than issues with default system functionality.
Limited or too wide of functionality. An add-on YMS module offers only a basic feature set, which may be insufficient if you provide a wide range of logistics services. On the other hand, standalone YMS solutions may have many features that are unnecessary for your business. For example, you may want your YMS to tell you when you need more spotters or organize shipments by priority. But in a ready-made add-on YMS module or standalone YMS, such features may be missing, or using them may require an additional monthly fee.
Arduous integration with software from different vendors. If you decide on an add-on YMS module, you may struggle to add it to your existing WMS or TMS. And if you choose a standalone YMS, you may have issues with exchanging data between this YMS and your other logistics systems.
In general, existing software options work well if a yard doesn’t require many custom configurations or specific adjustments. If you want your YMS to be highly tailored to your yard’s needs, consider developing custom software.
Custom YMS software: pros, cons, and examples
Logistics businesses have different expectations of their YMSs. For example, in the cross-docking reality of the retail industry, the speed of order execution and appointment management are the most important processes in the yard.
A custom software product developed with your needs and objectives in mind can result in better business performance and maximize profits. However, you should also be aware of common drawbacks.
Cons of a custom YMS:
- The cost of custom development varies across software development providers and may increase as you update and expand your product. Read on the difference between in-house and outsourcing software development companies to learn more about software development costs.
- Developing and implementing a custom software solution takes more time than integrating a ready-made solution.
However, the advantages of building custom YMS software more than outweigh the drawbacks.
Below are two real-world examples of how a custom YMS helps companies enhance the performance of their yards.
Arla Foods
Arla Foods needed an effective YMS for managing its new dairy manufactory with a fleet of 150 trucks. It was critical for Arla’s managers to efficiently track the vehicle flow in the yard 24/7 all year round.
Since the launch, Arla’s custom YMS has helped yard managers:
- reduce time on allocating parking spots to trucks
- minimize truck movements and dwell time
- automate instructions to yard drivers and truck drivers on all yard movements
Port of Gdansk
There were lots of uncontrolled movements in the yard at the port of Gdansk, and there was frequent gate congestion due to lots of trucks arriving at the same time. In response, the port implemented a custom YMS solution with real-time visibility of all trucks.
The software solution included custom scheduling and traffic management functionality for automated communication with truck drivers. This functionality also allowed all port personnel to book trucks for loading and unloading. As a result, the YMS reduced the average processing time of trucks at the gate from four minutes to four seconds.
An individual approach to development is beneficial, as the result is a solution that meets your expectations and solves your day-to-day challenges in the yard workflow. In the next section, we offer a few practical steps to take before developing an actual YMS solution.
Steps to build a proper custom YMS
If you’ve already decided to develop a custom YMS, there are three steps you should take before proceeding to development.
Step 1. Evaluate your current yard status
What you need here is the big picture of your current yard workflow to define areas you’re unsatisfied with. Describe the as-is state of each of the following yard aspects, including any details you consider important:
- yard size (number of docks and parking spots)
- shipment volume on a usual working day or week (whichever is easier for analysis)
- average spotter use on a usual working week or day
- gate management processes (e.g. manually managed or automated, frequency of gate congestion)
- dock operations (e.g. the frequency of delays in truck loading or unloading)
- practices for scheduling shipment appointments with carriers
Step 2. Identify correlations between the abovementioned yard constituents
Try to trace how one yard aspect you’ve analyzed in the previous step influences others to see the causal links between them and make conclusions about your yard performance.
For instance:
- The correlation between shipment volumes and yard size can show whether you’re using your yard capabilities to their fullest.
- Average spotter use indicates whether you have enough spotters to efficiently move your usual number of trailers between dock doors and parking spots.
- Frequent gate congestion may occur because of errors in phone-based shipment scheduling with carriers.
Step 3. Define YMS functionality based on your conclusions
After analyzing your yard, you can think of the possible features your YMS should include. For instance, you may realize that an online shipment appointment scheduling tool can solve most of the issues you face at the gate such as long truck dwell times. As a result, you may decide to work on the appointment scheduling tool first and test if you also need to develop gate management functionality.
That’s one of the perks of building a custom solution: you can avoid building even common features and see whether you actually need them over time.
Yalantis is here to back you up with an in-depth yard performance analysis to suggest areas for improvement and just the right set of functionality for your particular business case. We strive to deliver successful custom supply chain solutions that help our customers boost profits, decrease expenses, eliminate human error, and enhance services.
Want your yard to be more productive?
We can ensure it is with a custom software solution.
Rate this article
5/5.0
based on 1,106 reviews